Truck intercoolers, also known as charge air coolers or air coolers, play a vital role in optimizing the performance of heavy-duty vehicles. Understanding their working principle and the impact of different manufacturing processes on their installation efficiency is crucial. In this blog post, we will delve into the intricacies of truck intercoolers, exploring their function and how various manufacturing techniques can affect their effectiveness when installed in trucks. Let’s explore the world of intercoolers, a key truck part, and their significance in maximizing performance.
The Working Principle of Intercoolers:
Intercoolers are heat exchangers that cool the compressed intake air from the turbocharger before it enters the engine’s combustion chamber. Compressed air tends to heat up during the process, reducing its density and overall combustion efficiency. Intercoolers utilize ambient air or external cooling mechanisms to lower the temperature of the compressed air, increasing its density and optimizing engine performance.
Different Manufacturing Processes:
Intercoolers are manufactured using various techniques, each with its own advantages and considerations. Common manufacturing processes include tube and fin, bar and plate, and stacked plate designs. These techniques determine the construction, performance, and efficiency of the intercooler.
Tube and Fin Intercoolers:
Tube and fin intercoolers feature a series of small tubes connected to fins. Compressed air flows through the tubes, while ambient air passes through the fins, facilitating heat transfer. This design offers a balance between cooling efficiency and compact size, making it suitable for applications with limited space. However, tube and fin intercoolers may have higher pressure drop and lower heat transfer capabilities compared to other designs.
Bar and Plate Intercoolers:
Bar and plate intercoolers consist of a series of flat plates separated by bars. Compressed air passes through the interconnecting passages between the plates, while ambient air cools the plates themselves. This design provides excellent heat transfer efficiency, low pressure drop, and greater durability. Bar and plate intercoolers are commonly used in high-performance applications due to their superior cooling capabilities.
Stacked Plate Intercoolers:
Stacked plate intercoolers utilize a series of flat plates stacked together, forming multiple channels for airflow. The compressed air passes through the channels while ambient air cools the plates. Stacked plate intercoolers offer excellent cooling efficiency, compact size, and reduced pressure drop. They are often preferred for applications where space is limited, such as in trucks.
Impact on Installation Efficiency:
The choice of intercooler design and manufacturing process greatly affects the installation efficiency in trucks. Factors such as size, weight, and compatibility with the truck’s existing systems are crucial considerations. Manufacturers optimize intercoolers to ensure a proper fit and seamless integration with specific truck models, maximizing installation efficiency and minimizing the need for modifications.
Manufacturer Selection:
When choosing an intercooler for a truck, it is essential to select a reputable manufacturer. Trusted manufacturers adhere to strict quality control standards, ensuring that their intercoolers meet or exceed industry requirements. Researching manufacturer reputation, customer reviews, and warranty coverage can provide insights into the reliability and performance of the intercoolers they produce.
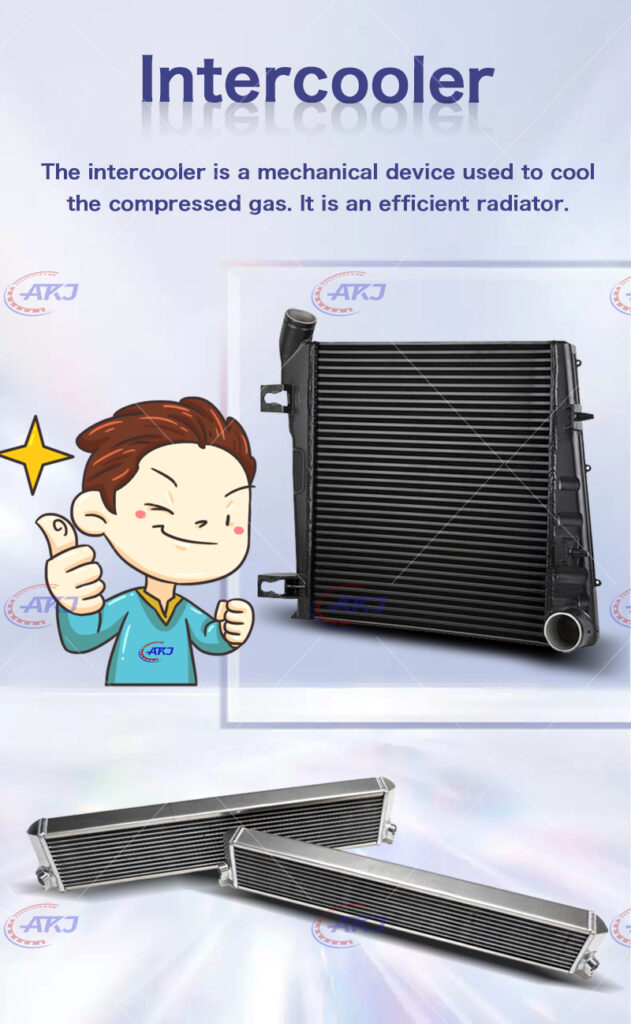