In the world of construction machinery, the cooling system plays a crucial role in maintaining optimal engine performance. When it comes to aftermarket cooling system parts like the EGR (Exhaust Gas Recirculation) cooler for the CUMMINS ISB6.7 engine, understanding the various welding processes involved is essential. In this blog post, we will delve into the welding techniques commonly used in factory-produced construction machinery EGR coolers, focusing on vacuum brazing, continuous brazing, TIG welding, and the choice of internal pipe (corrugated pipe or threaded pipe). By exploring these welding processes, we can better comprehend the intricacies and benefits associated with each technique.
Vacuum Brazing:
Vacuum brazing is a precise and controlled welding process widely used in the manufacturing of EGR coolers for construction machinery. This technique involves heating the joint area under vacuum conditions while introducing a brazing filler material. The absence of air prevents oxidation during the brazing process, resulting in strong and leak-free joints.
Benefits of Vacuum Brazing:
Superior Joint Strength: Vacuum brazing produces strong, durable joints with excellent mechanical properties. The process ensures tight bonding between the base metal and the brazing filler material, resulting in high joint integrity.
Enhanced Heat Transfer: The vacuum environment allows for uniform heat distribution, ensuring efficient heat transfer throughout the EGR cooler. This promotes optimal cooling performance and helps maintain engine efficiency.
Minimal Distortion: Vacuum brazing minimizes distortion and deformation of the EGR cooler, ensuring dimensional accuracy and proper fitment within the cooling system.
Reduced Corrosion Risk: The absence of oxygen during the brazing process reduces the risk of corrosion, enhancing the longevity and reliability of the EGR cooler.
Continuous Brazing:
Continuous brazing is another commonly employed welding technique for factory-produced EGR coolers in construction machinery. This process involves passing the EGR cooler through a continuous furnace, where it is heated to the brazing temperature while continuously introducing the brazing filler material.
Benefits of Continuous Brazing:
Efficient Production: Continuous brazing allows for high-volume production with consistent quality and repeatability. The automated nature of this process facilitates faster production cycles and increased productivity.
Cost-Effectiveness: Continuous brazing offers cost advantages due to its high-speed production capabilities and minimal labor requirements. This makes it an ideal choice for large-scale manufacturing of EGR coolers.
Uniform Heating: The continuous furnace ensures uniform heating of the EGR cooler, resulting in consistent brazing throughout the assembly. This helps achieve reliable and leak-free joints.
TIG Welding:
Tungsten Inert Gas (TIG) welding is a versatile welding process often utilized in the fabrication of EGR coolers for construction machinery. TIG welding employs a non-consumable tungsten electrode to create an electric arc that melts the base metal and filler material, forming a solid joint.
Benefits of TIG Welding:
Precision and Control: TIG welding allows for precise control over the welding process, making it suitable for intricate and critical joints in the EGR cooler. The operator can adjust the heat input and welding parameters to achieve optimal results.
Weld Quality: TIG welding produces high-quality welds with minimal spatter, porosity, and distortion. This results in strong and aesthetically pleasing joints, ensuring the integrity and reliability of the EGR cooler.
Versatility: TIG welding can be used with various materials commonly found in EGR coolers, including aluminum and stainless steel. This versatility enables manufacturers to meet specific requirements and achieve desired performance characteristics.
Choice of Internal Pipe:
a) Corrugated Pipe: Corrugated internal pipes in EGR coolers provide several advantages. The corrugations increase surface area, promoting efficient heat transfer and enhancing cooling performance. Additionally, the flexibility of corrugated pipes allows for better thermal expansion and contraction, reducing stress on the assembly.
b) Threaded Pipe: Threaded internal pipes offer their own set of benefits. The threads create turbulence within the coolant flow, improving heat transfer and reducing the risk of deposits and clogging. Threaded pipes also provide structural strength and stability to the EGR cooler assembly.
In the realm of factory-produced construction machinery EGR coolers, welding processes play a critical role in ensuring performance, durability, and reliability. Vacuum brazing and continuous brazing provide strong joints, efficient heat transfer, and corrosion resistance. TIG welding offers precision, versatility, and high-quality welds. The choice between corrugated and threaded internal pipes depends on specific design considerations and performance requirements. By understanding these welding techniques and their associated benefits, manufacturers can produce aftermarket cooling system parts that meet the demanding needs of construction machinery, ensuring optimal engine performance and reliability in the field.
contact us: safenna@pgakj.com
Welding Processes Construction Machinery EGR Cooler for CUMMINS ISB6.7
Welding Processes Construction Machinery EGR Cooler for CUMMINS ISB6.7
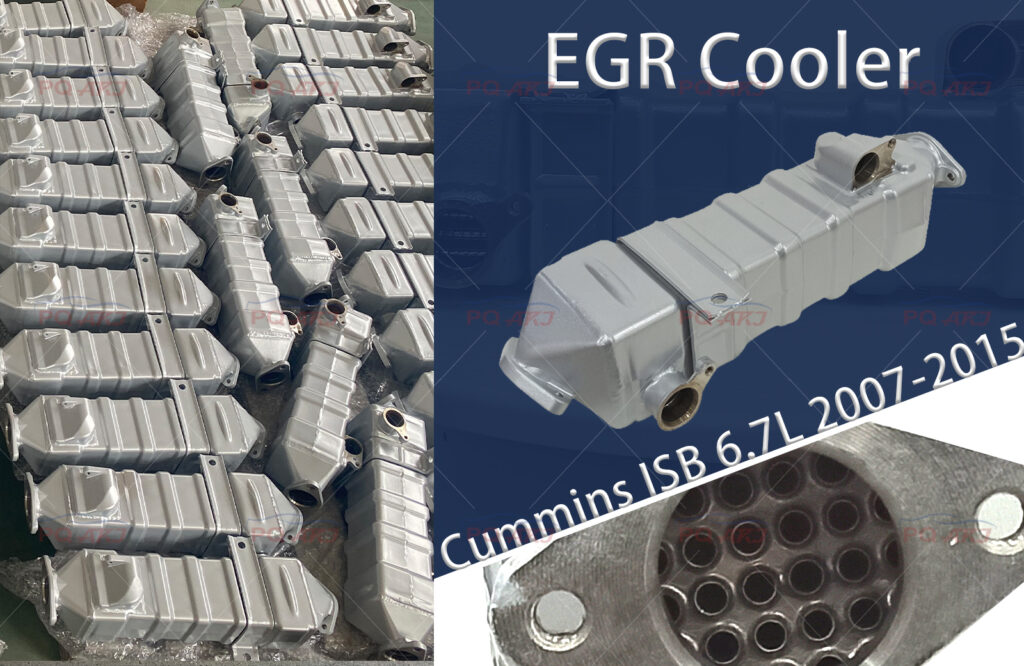